Hey everyone, it’s been quite a while since I’ve done a printer review. We’ve been in the process of moving house (after living in a shed for 2 months) and oh it has been a crazy time!
Artillery makes all of my favourite printers that I own, so I am very excited that they wanted to send me their new unit to do a review on. Their machines are generally very fell finished off, and come out of the box ready to print with only a minor assembly.
The other thing I like about artillery printers is that they generally require no modifications, they come with directdrive titan extruders, have silent steppers and mainboard and all the jazz to go with it!
Unboxing
Okay let’s get to unboxing this printer, it came straight from Artillery, and the box is pretty much fully intact and even plastic wrapped which is nice since it was raining when the printer got delivered.
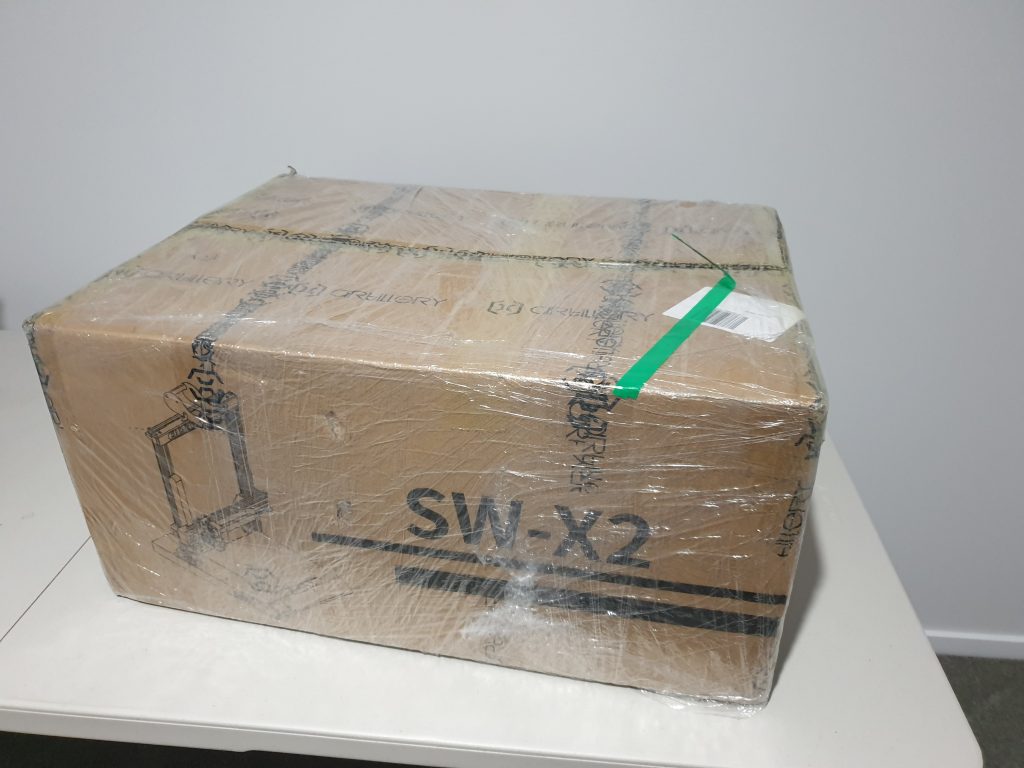
After removing the plastic wrap:
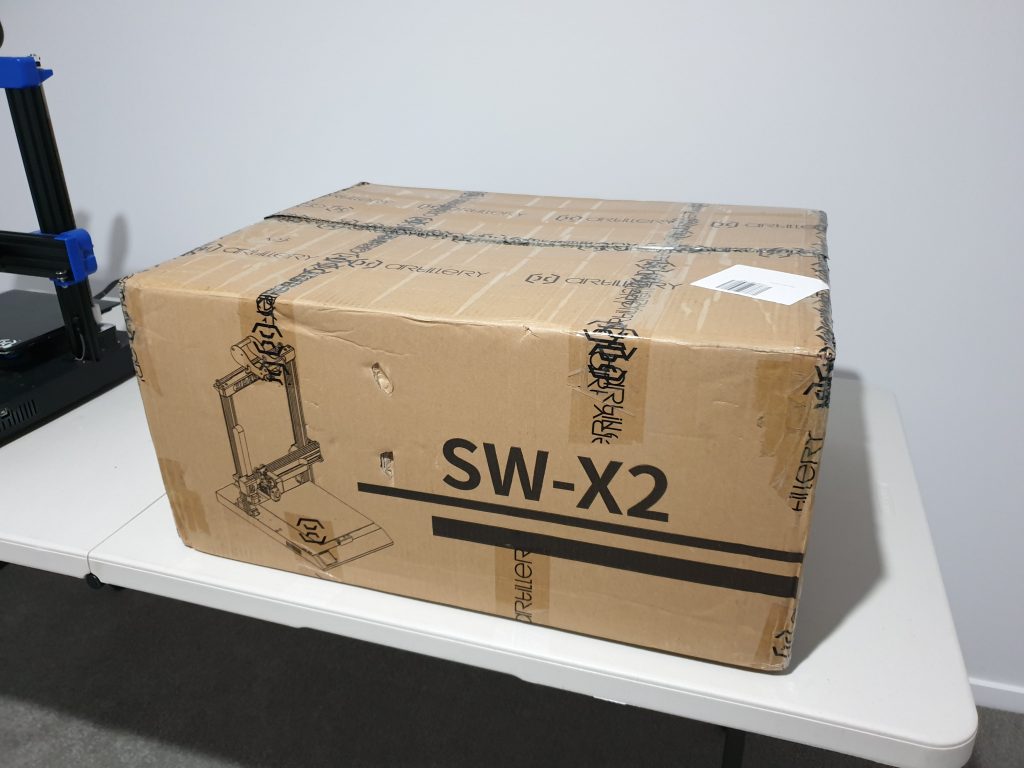
The inside of the box looks basically identical to the Sidewinder X1, which makes sense.. If it aint broke don’t fix it hey! The structure of the printer is basically the same so no need to change the packaging layout.
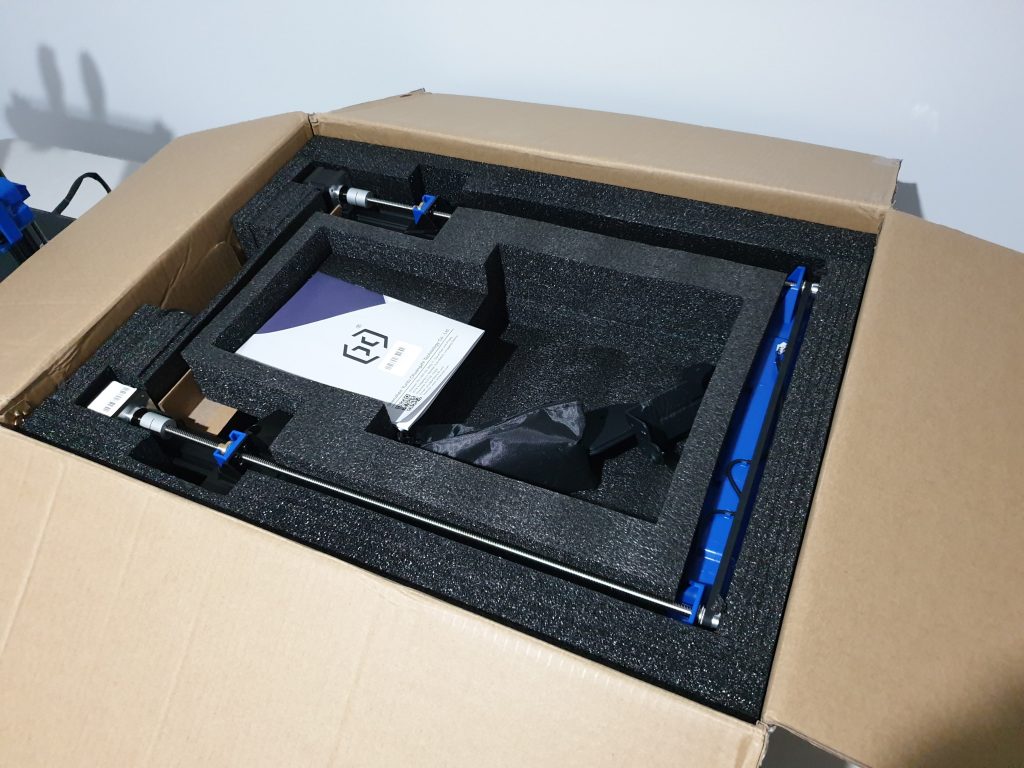
After removing the little container foam in the top the bed is uncovered
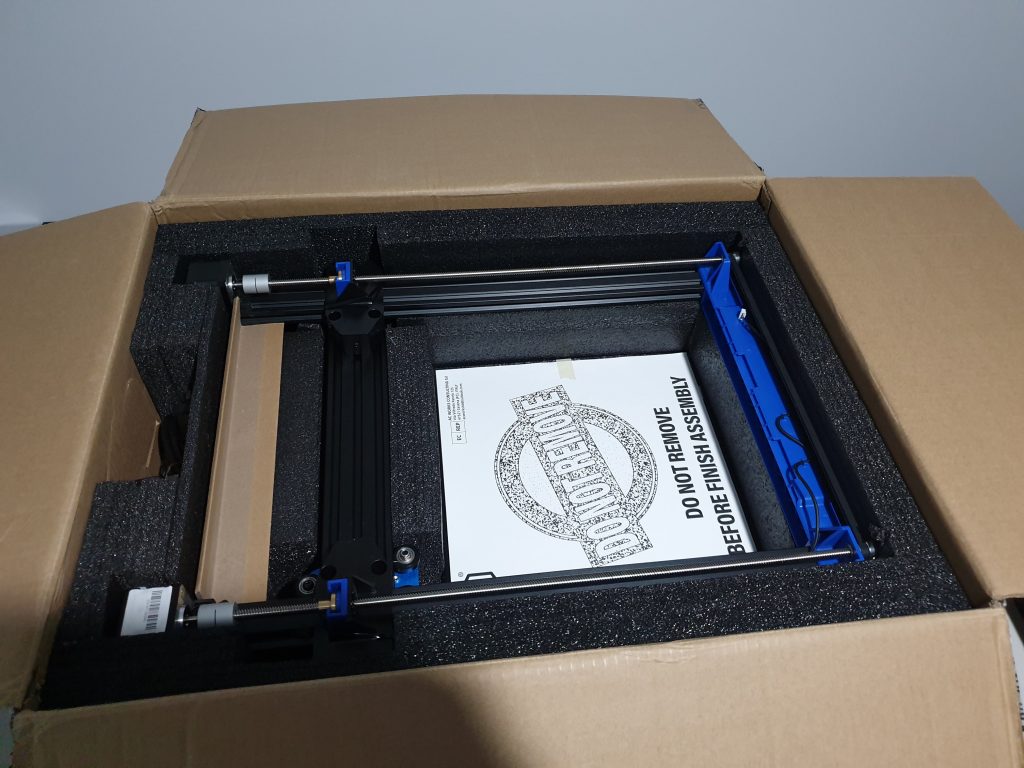
Then I pulled the gantry out and all that remains is the base of the printer
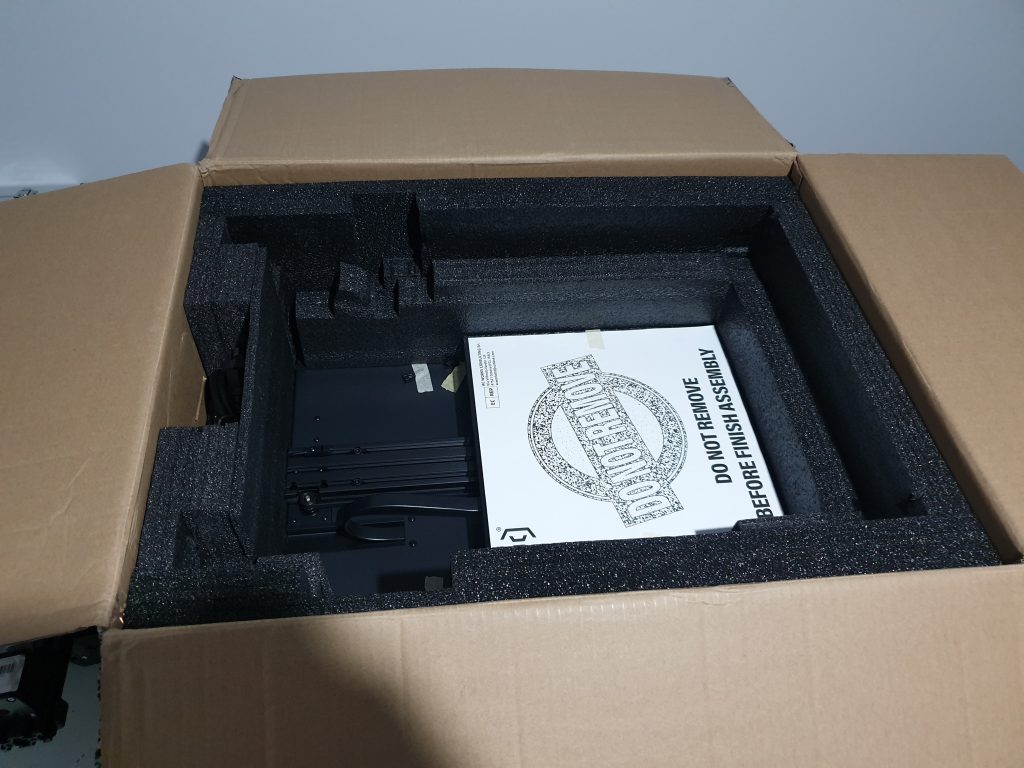
Here is everything from the box on the bench, not many parts which means this assembly will be a BREEZE!
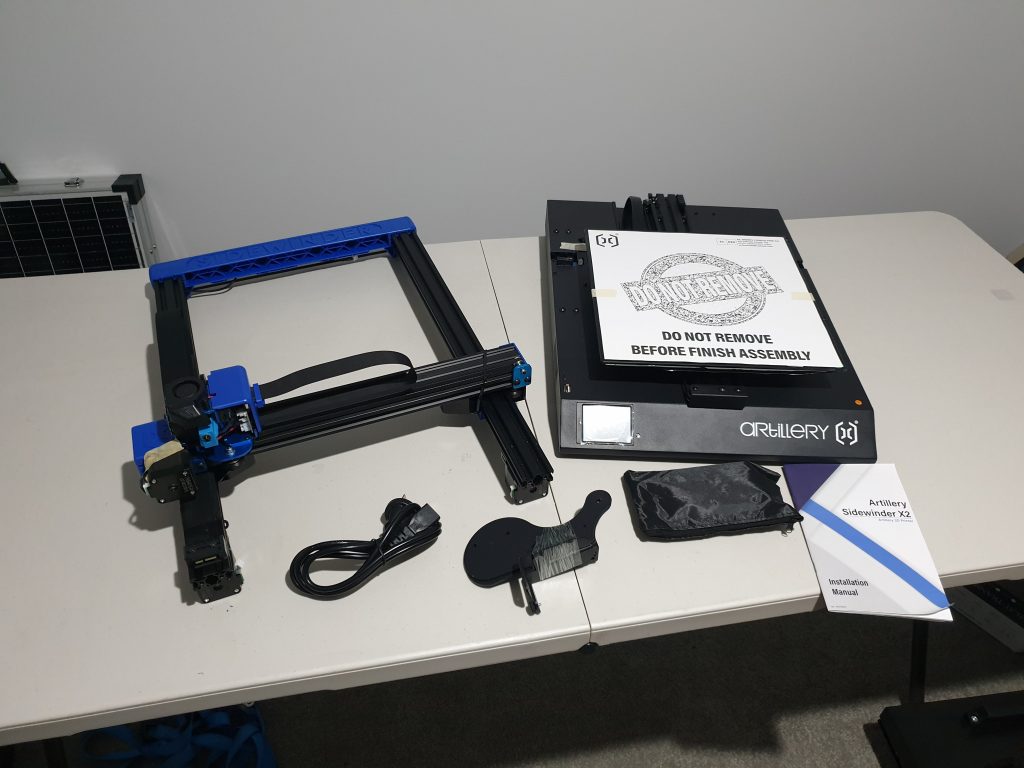
MANUAL
Next up we will take a look at the manual, which is generally another of artillerys strong points.
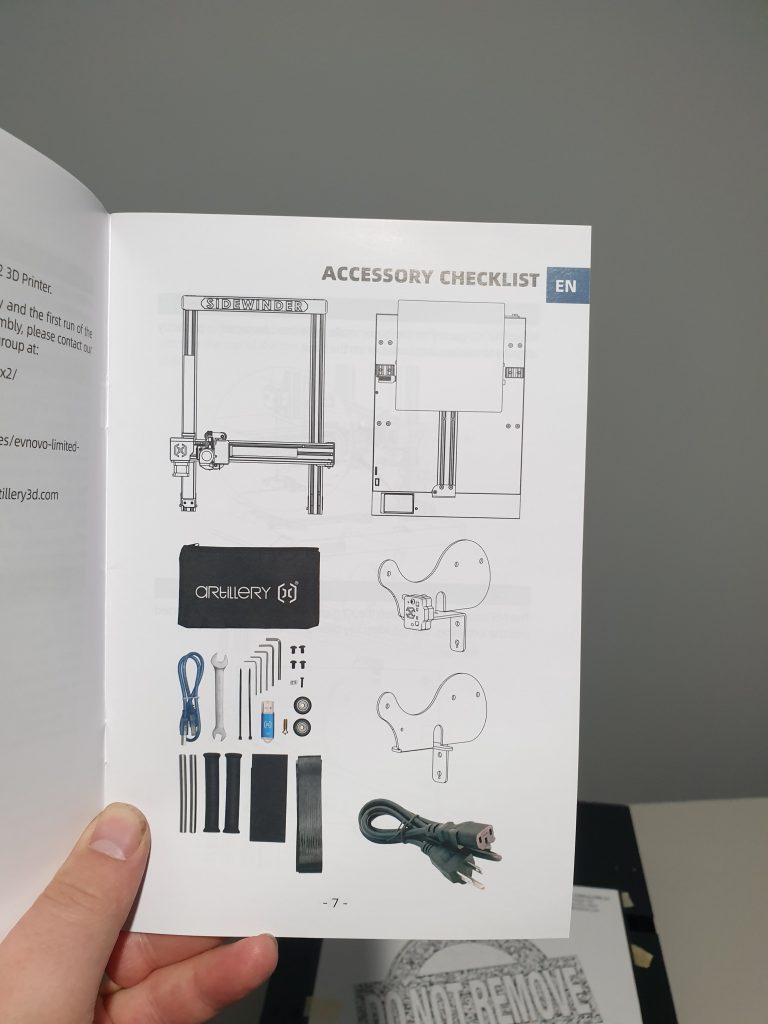
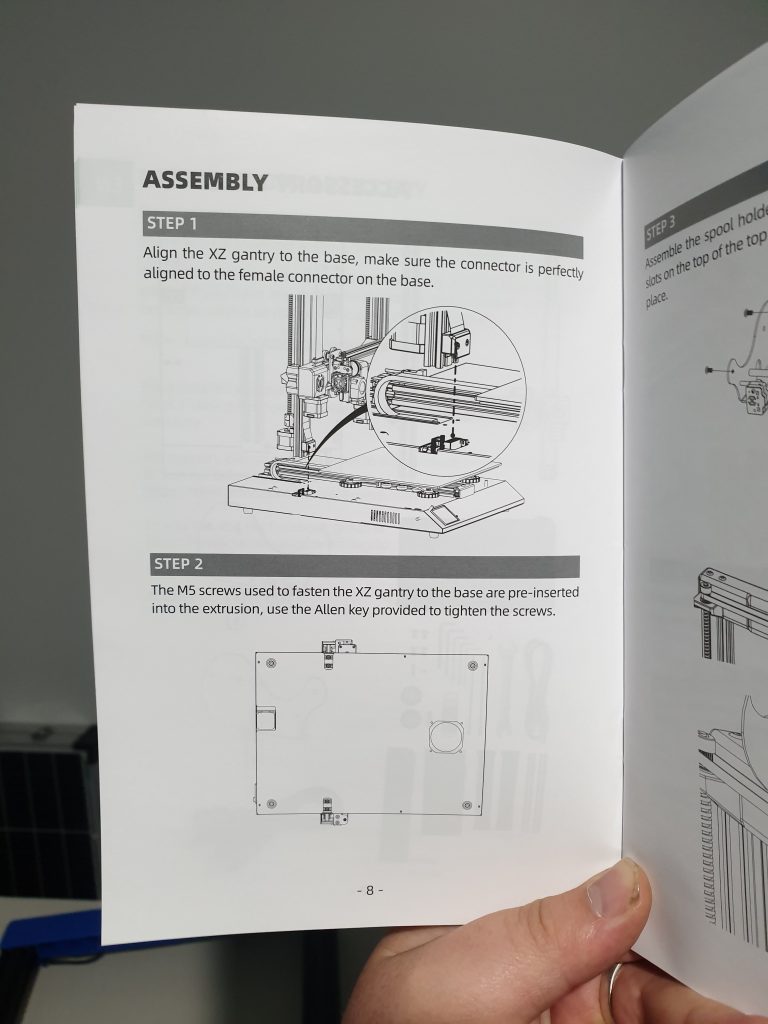
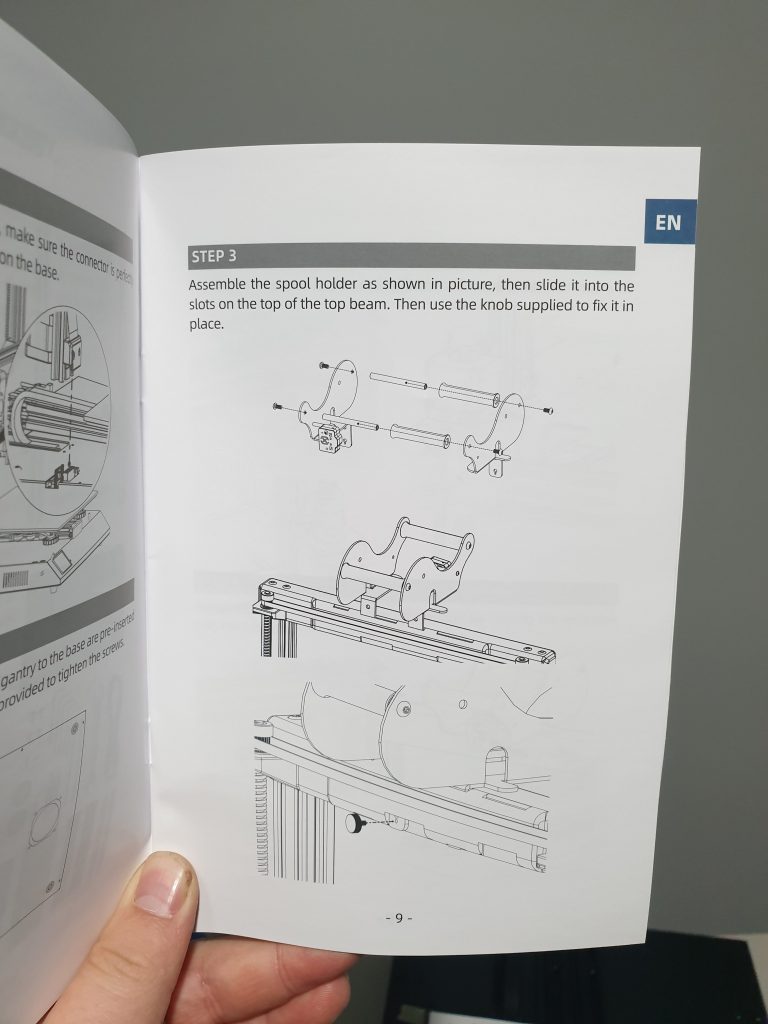
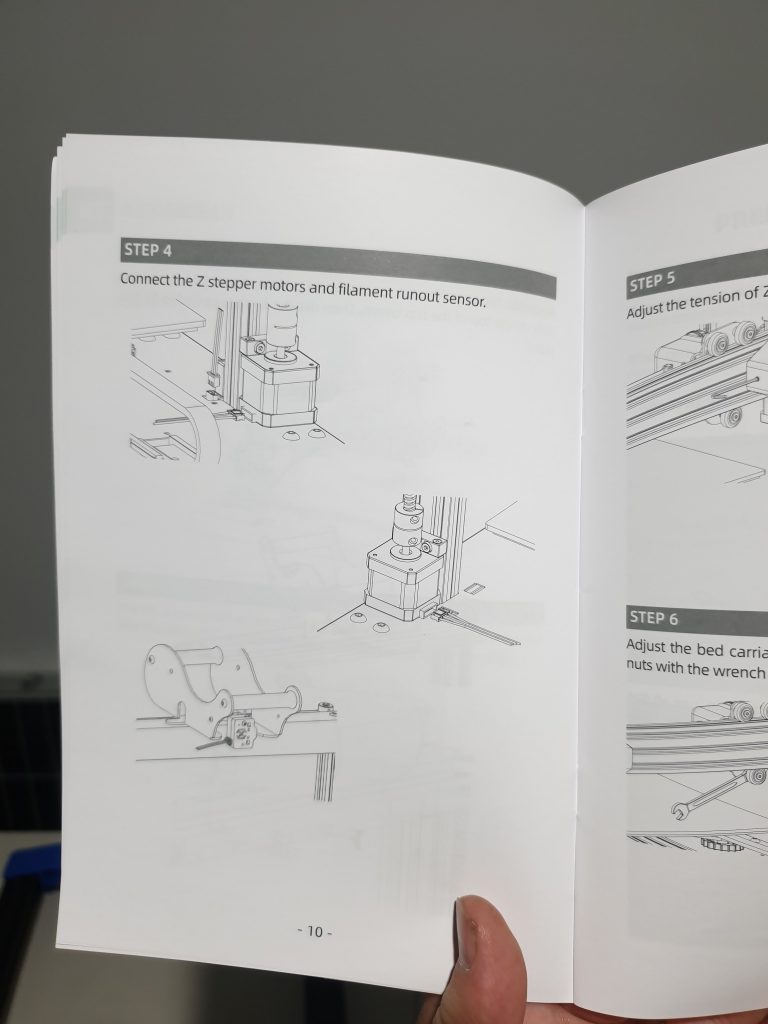
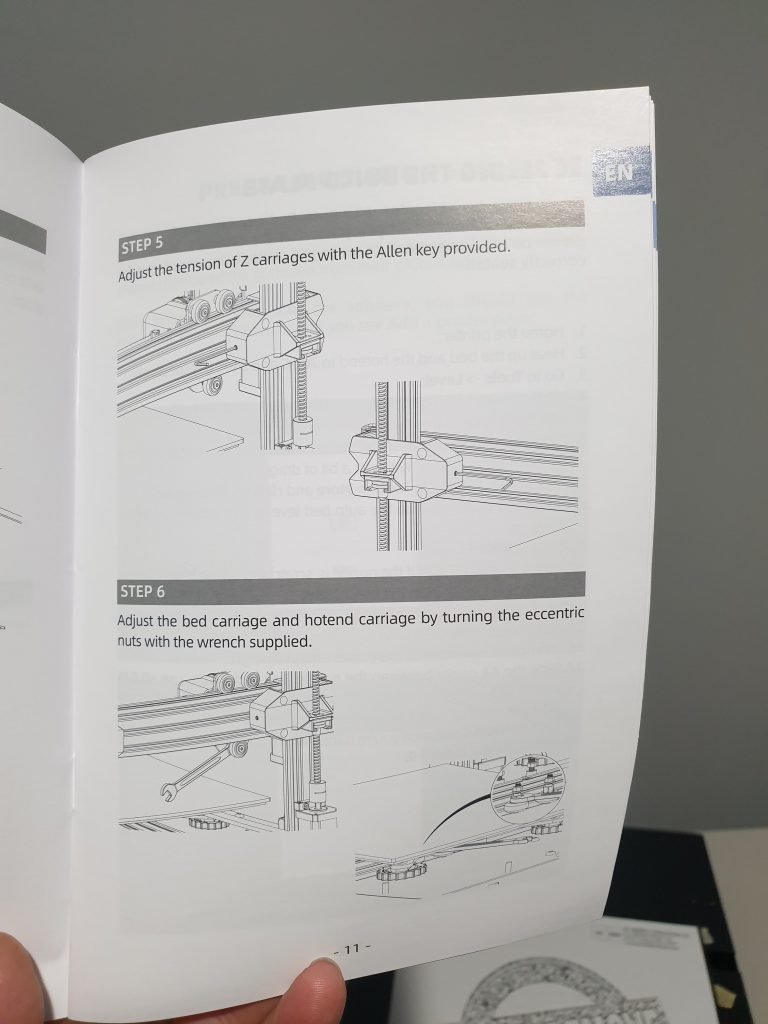
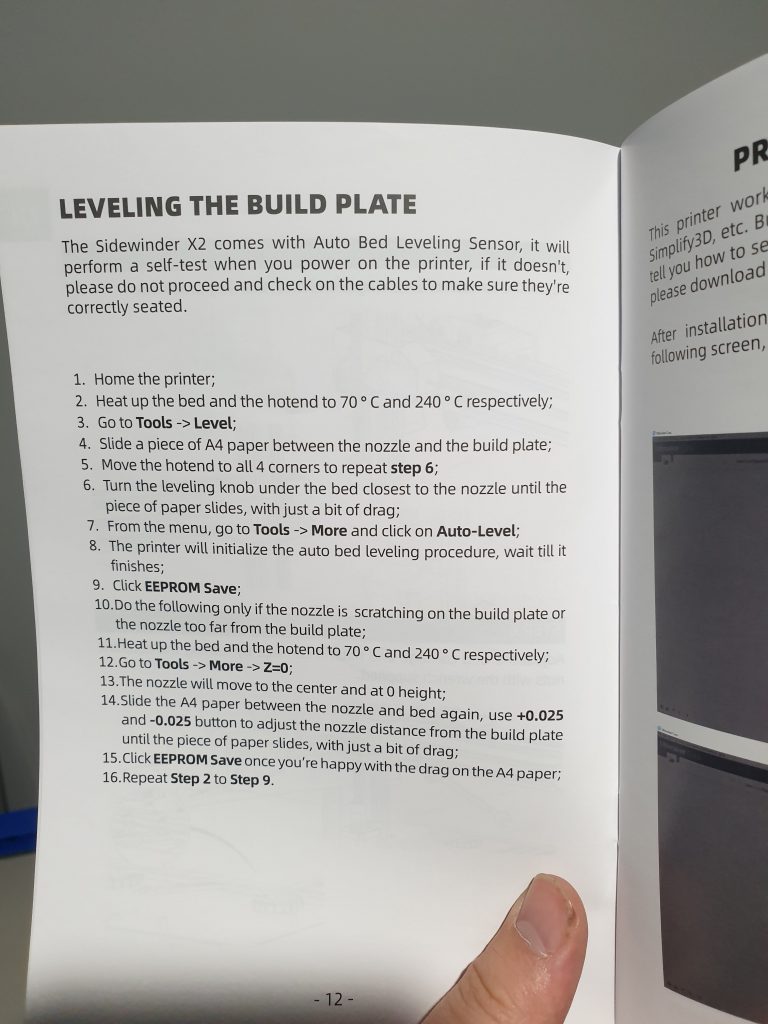
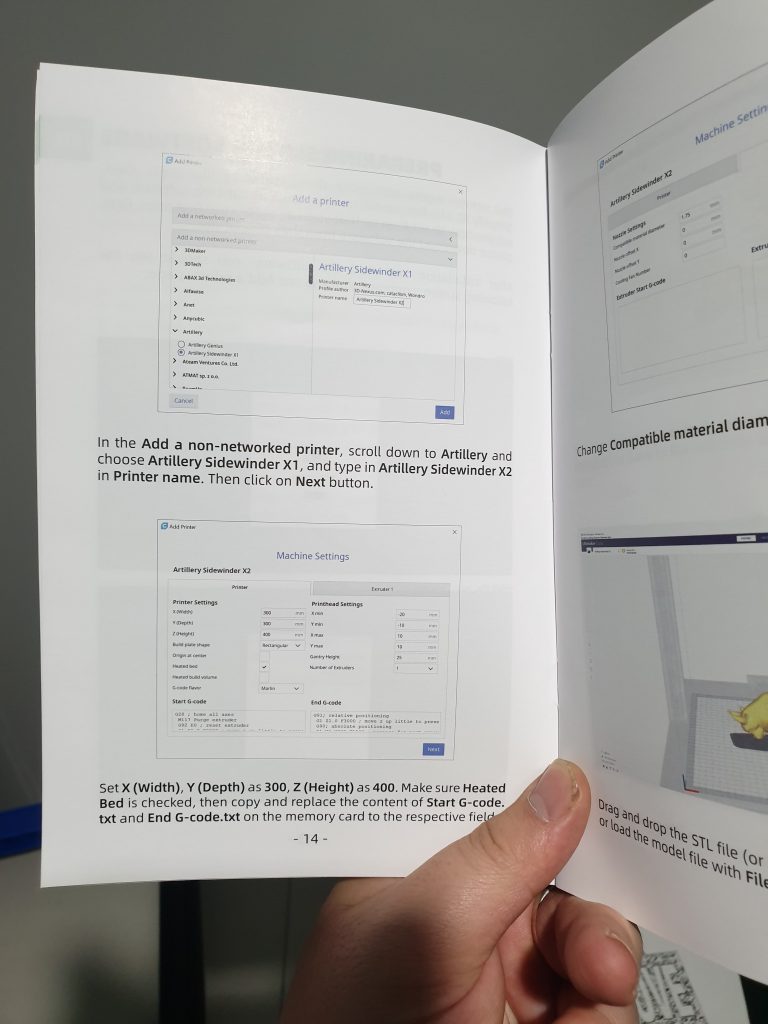
Assembly
First order of call for the assembly was attach the gantry, this can be a little awkward generally, but if you put the base on its side and attach it all laying on its side it is pretty easy. Here’s a pic with the gantry attached and the 4x M5 screws tightened.
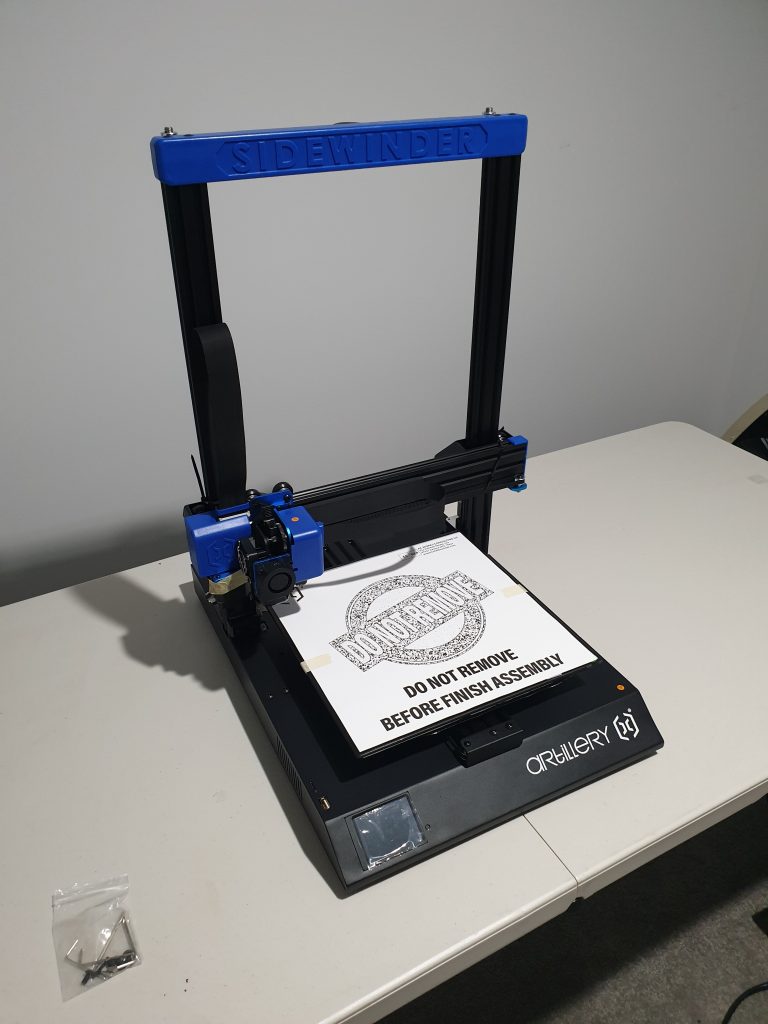
Next up was the spool holder, which basically just slips in and then you put in a little screw to hold it in place
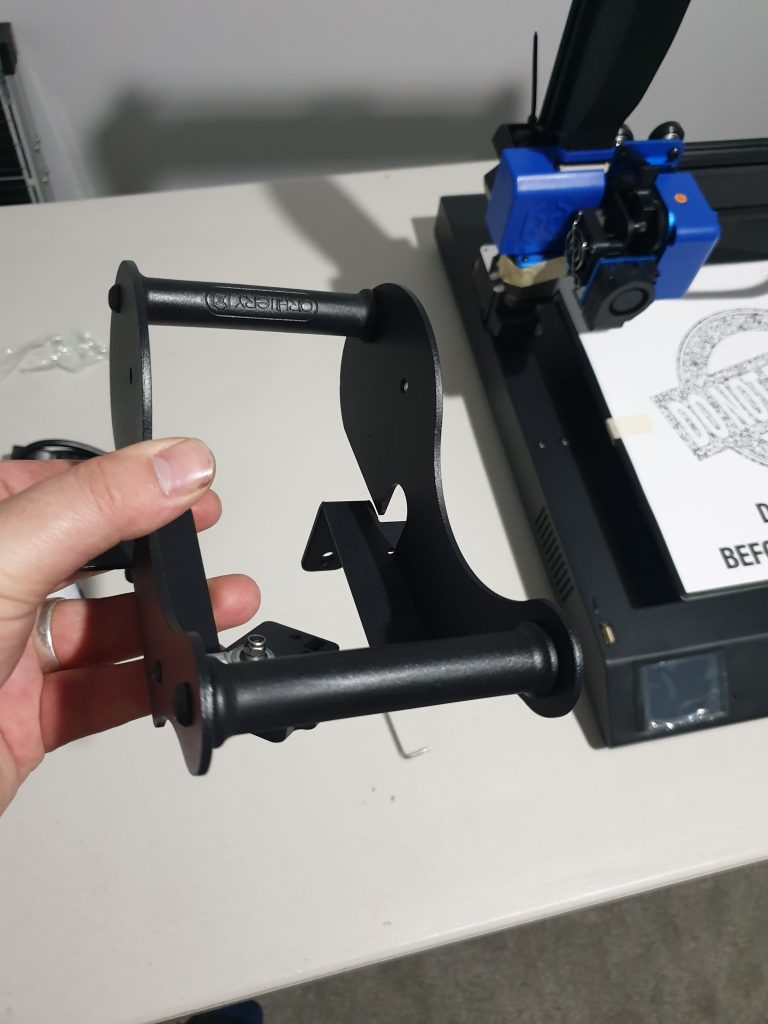
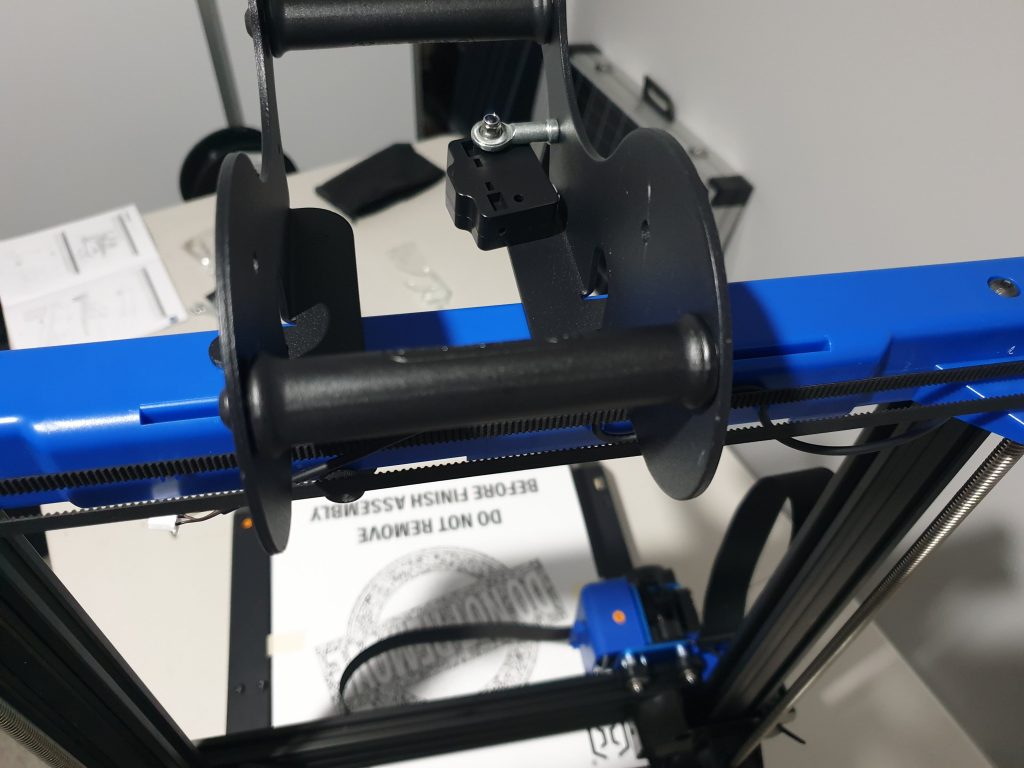
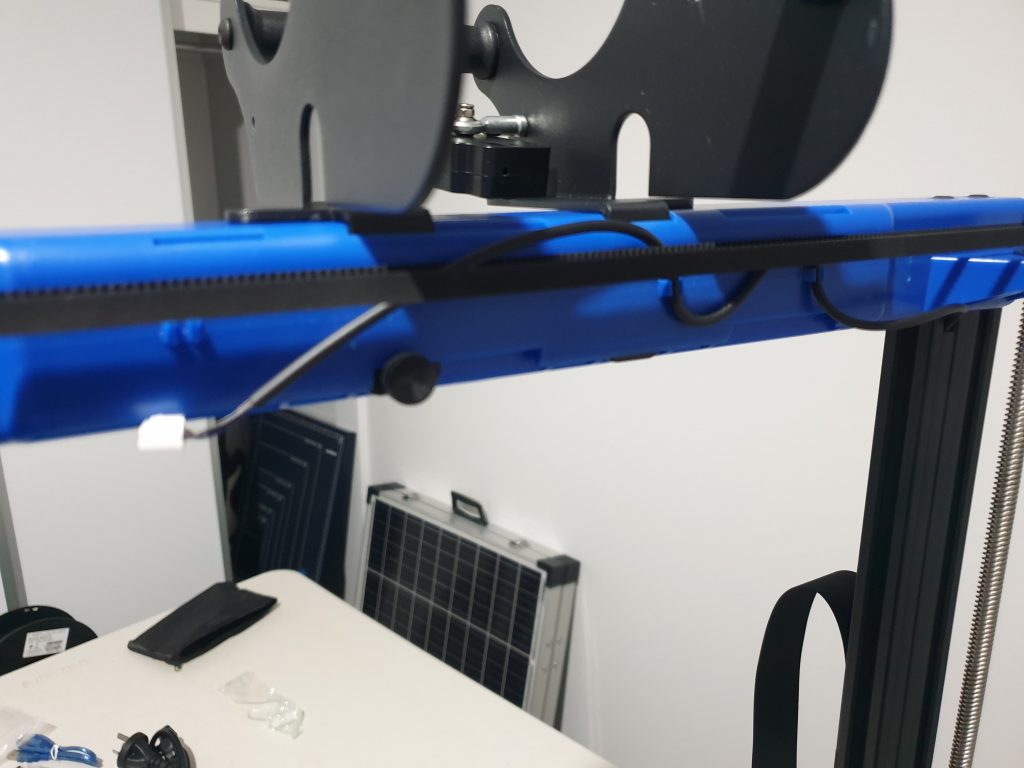
Plugged in the filament runout sensor
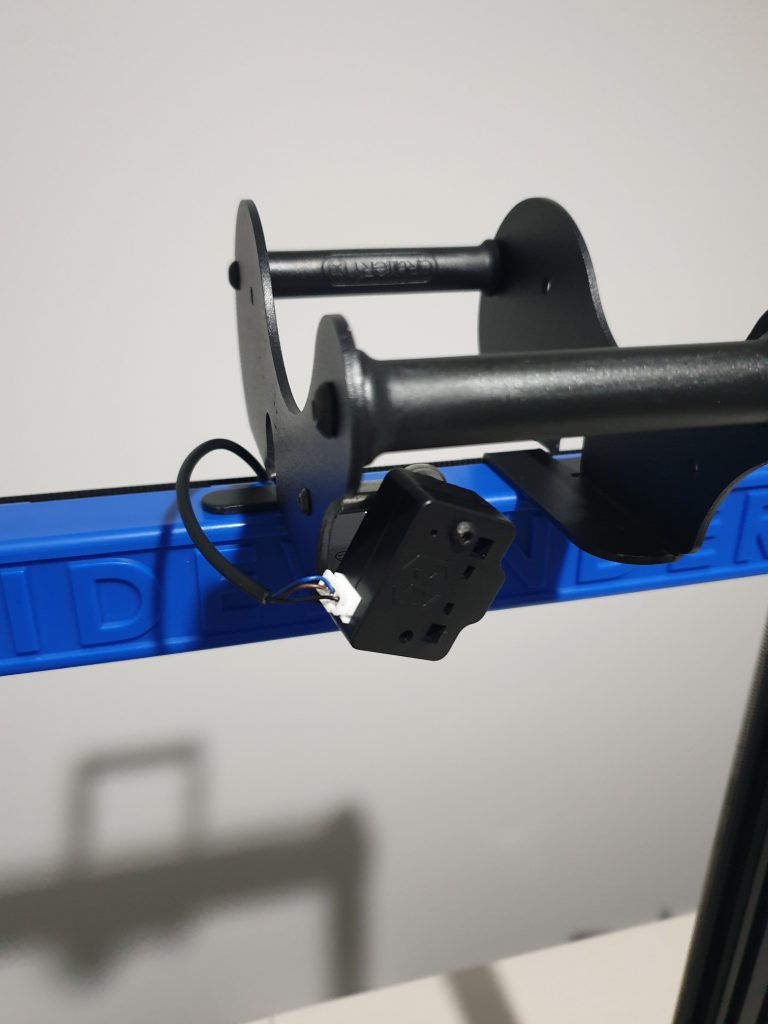
Next up was to plug in the rest of the cables as per the manual. They are all pre-wired and in the right place, so it’s pretty easy to do.
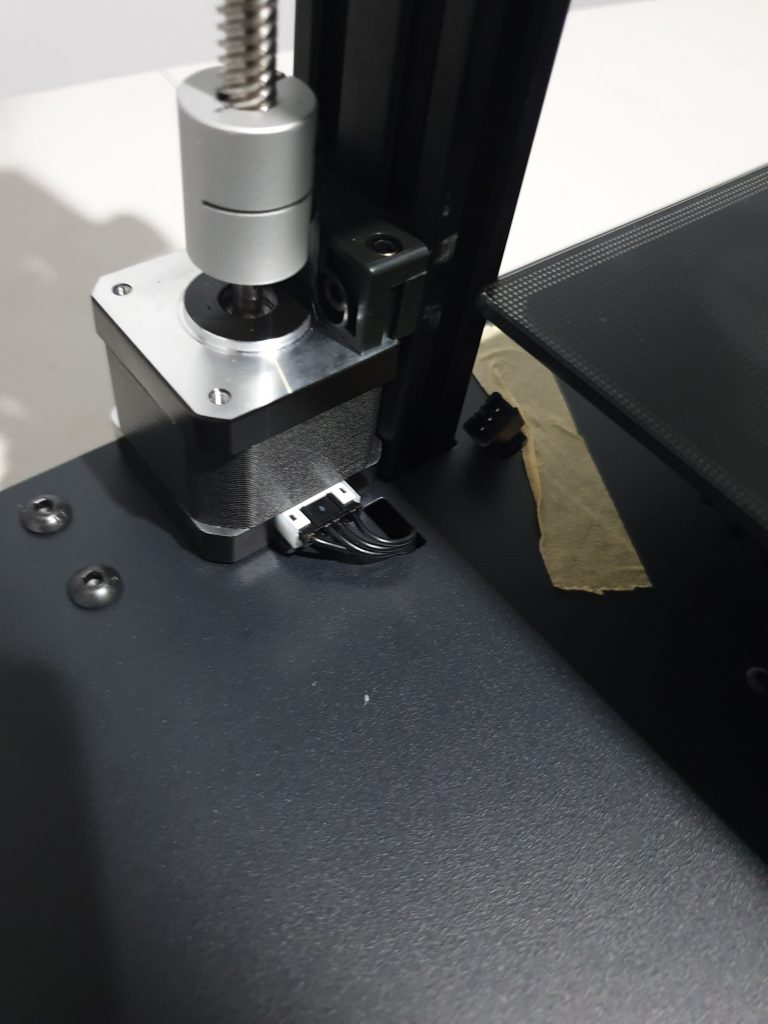
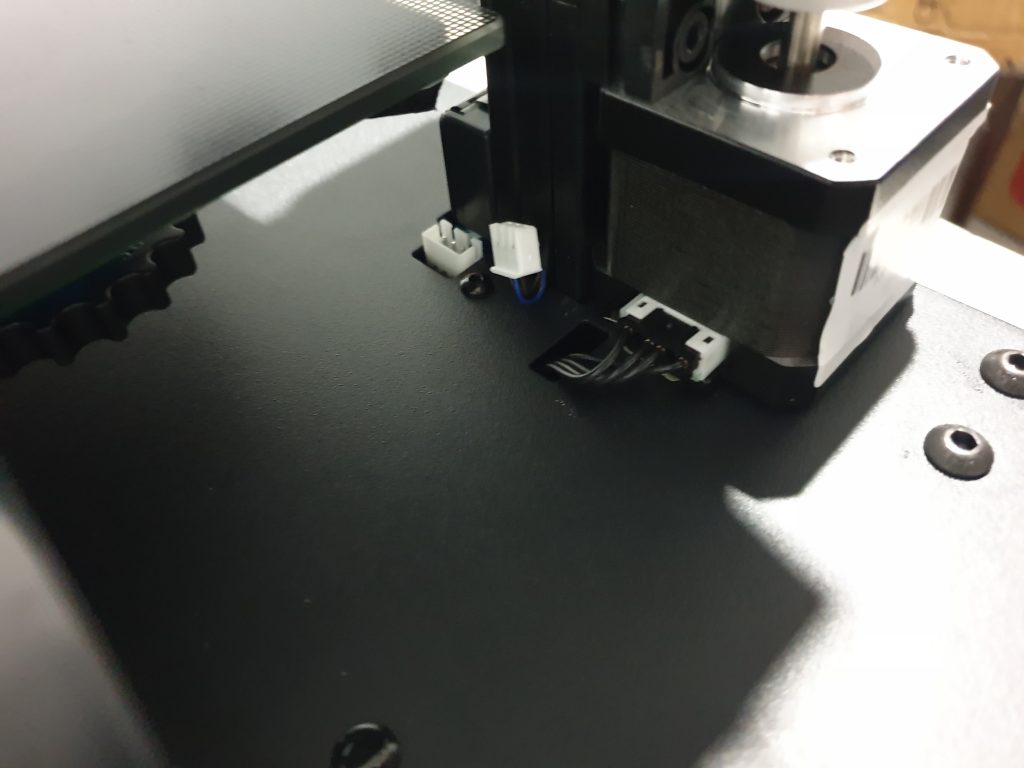
And here is the assembled printer, it is a nice looking printer if I may say so. It’s basically just a bigger Genius with some newer features which is nice.
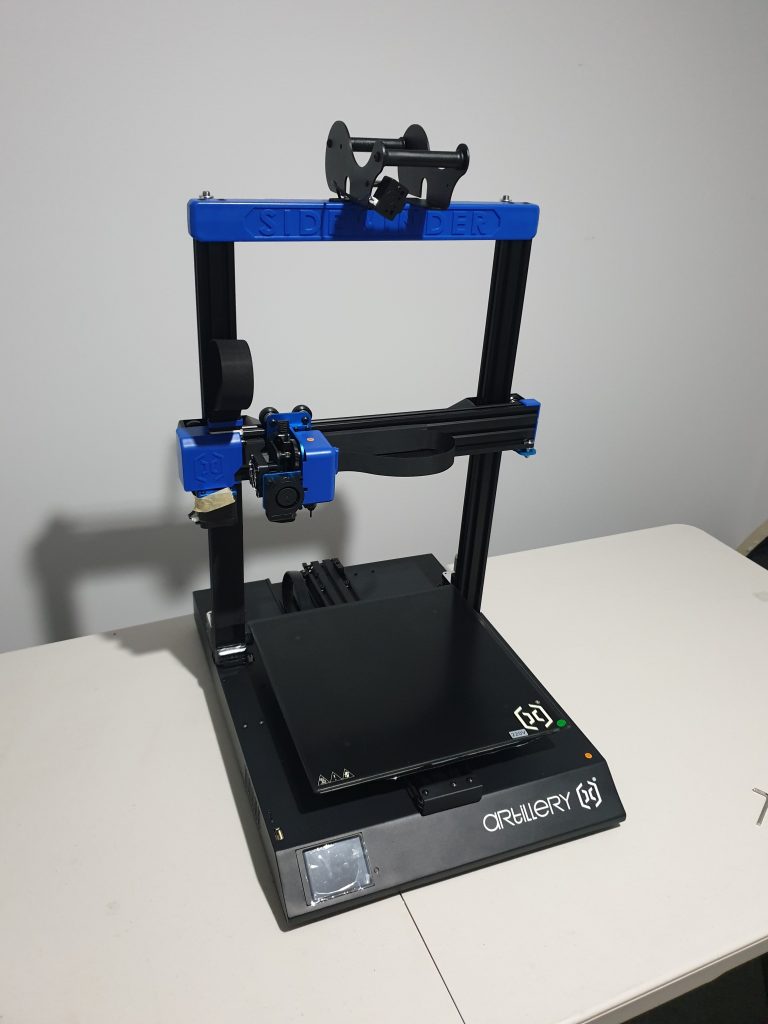
Here it is next to the genius, a lot of similarities!!
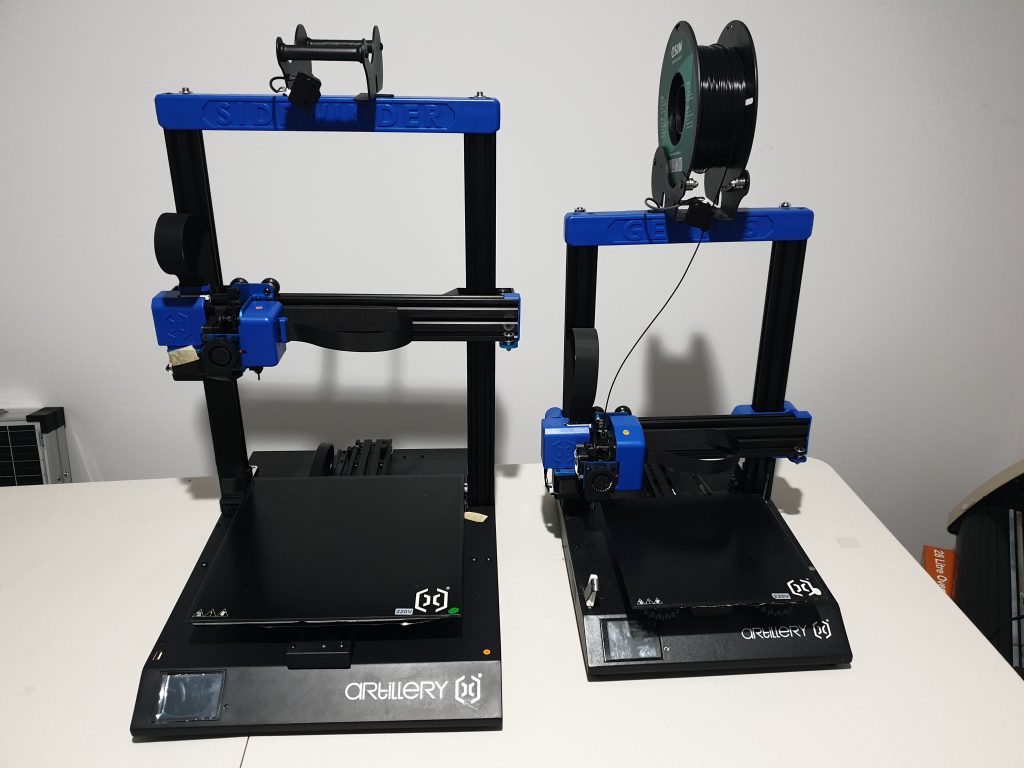
First Print
I am going to do a test print to show how this machine prints, so I put it on my racking system in my print room, Here I don’t run the filament on the printers mounts but instead on some printed mounts that hang off of my racking system.
In the past I have printed my own design of roller so that I can feed filament from my mounts through the runout sensor on artillery printers, but this new spool holder is designed in a way that I don’t have to which is neat!
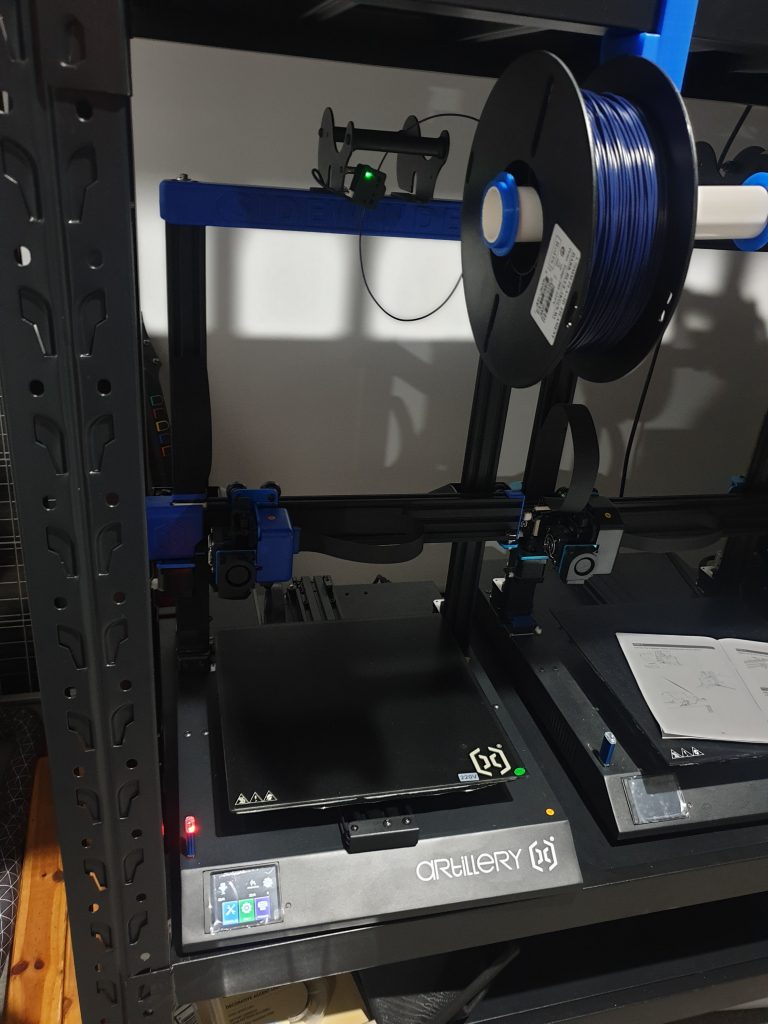
I went to start the print, but the normal artillery test print wasn’t on the USB, possibly because this is an early review unit. So I pulled the USB from my Sidewinder X1 since all the slicer settings should be the same and did the test print off of that USB using some dark Blue ESun PLA+.
During the print I noticed only one issue, and that was that the X axis gear was rubbing on the plastic cover. I just pulled the cover out a bit with my finger and it stopped so that’s good.
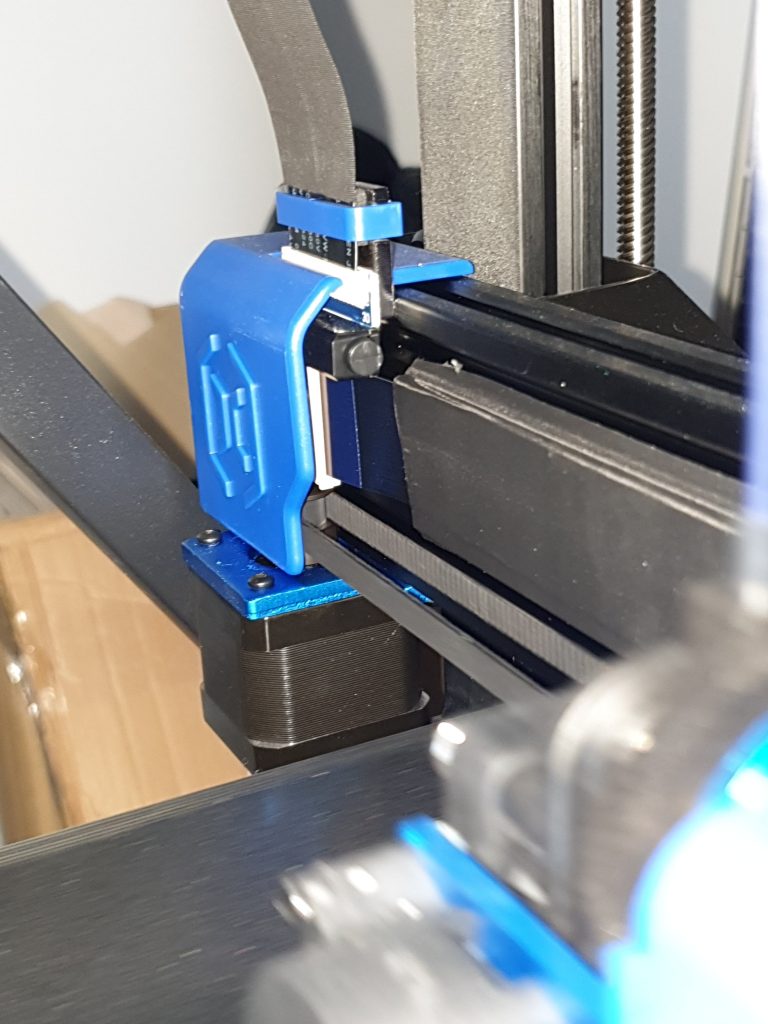
Here you can see the gear that sits very close to the cover.
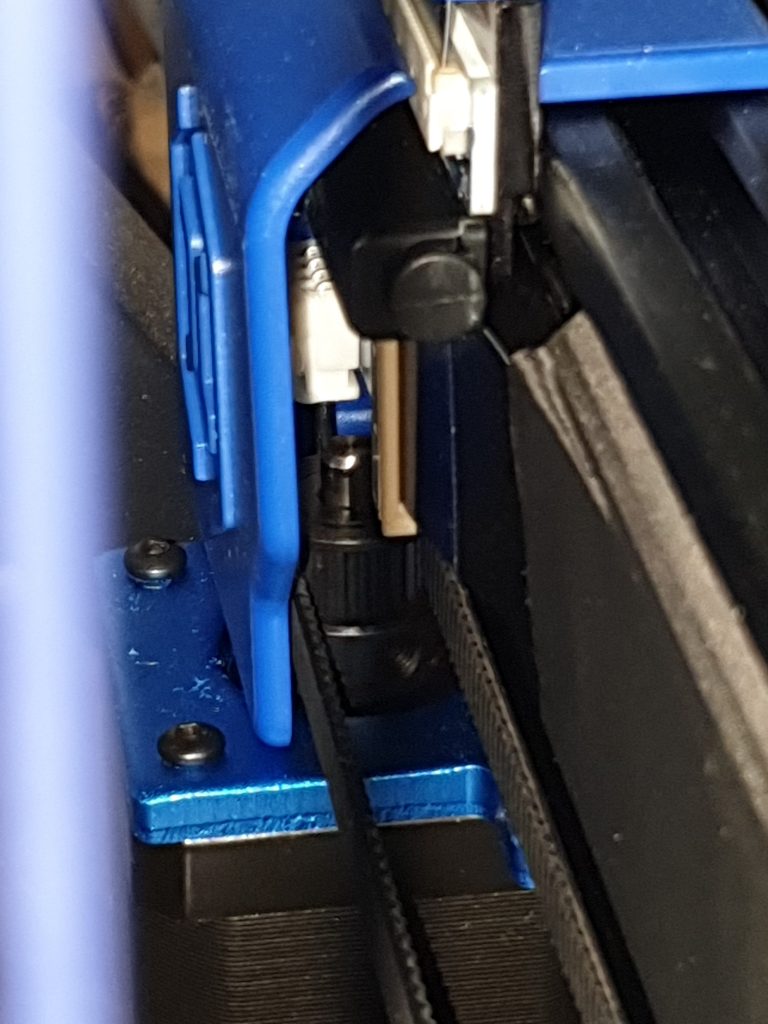
One of the cool included features of this printer is the auto bed levelling, in this picture you can see the sensor, which looks like a black version of a BL-Touch
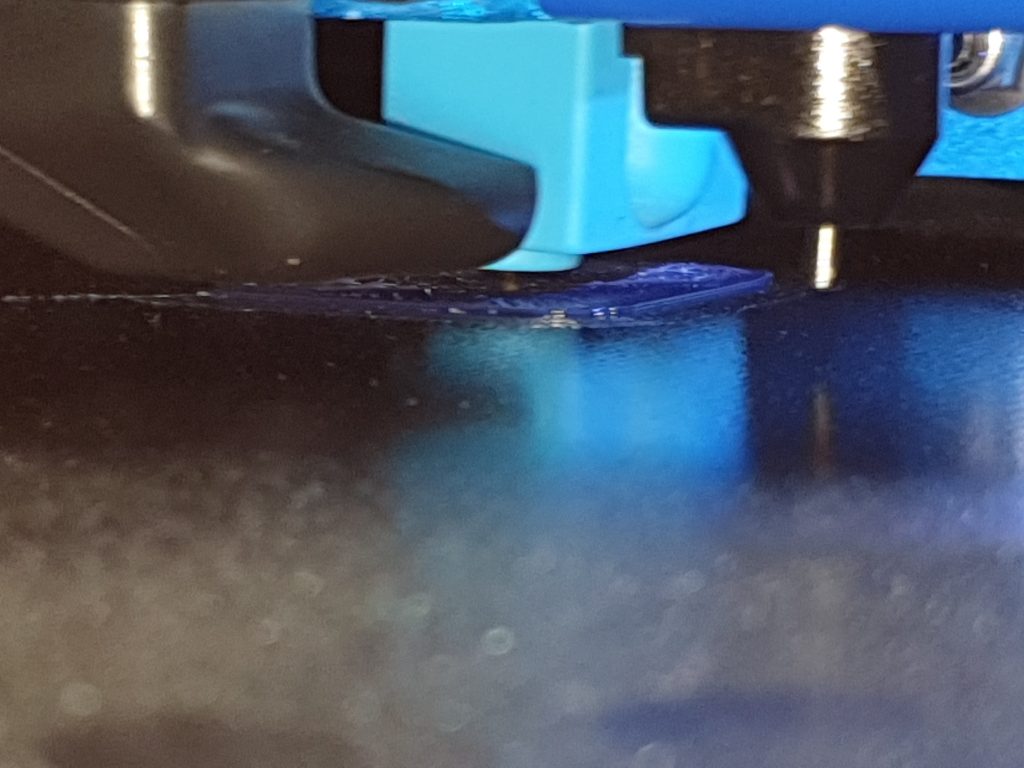
And here is the finished test print. For the first print after unpacking this printer and doing basically no tuning, I think that’s a pretty nice result.
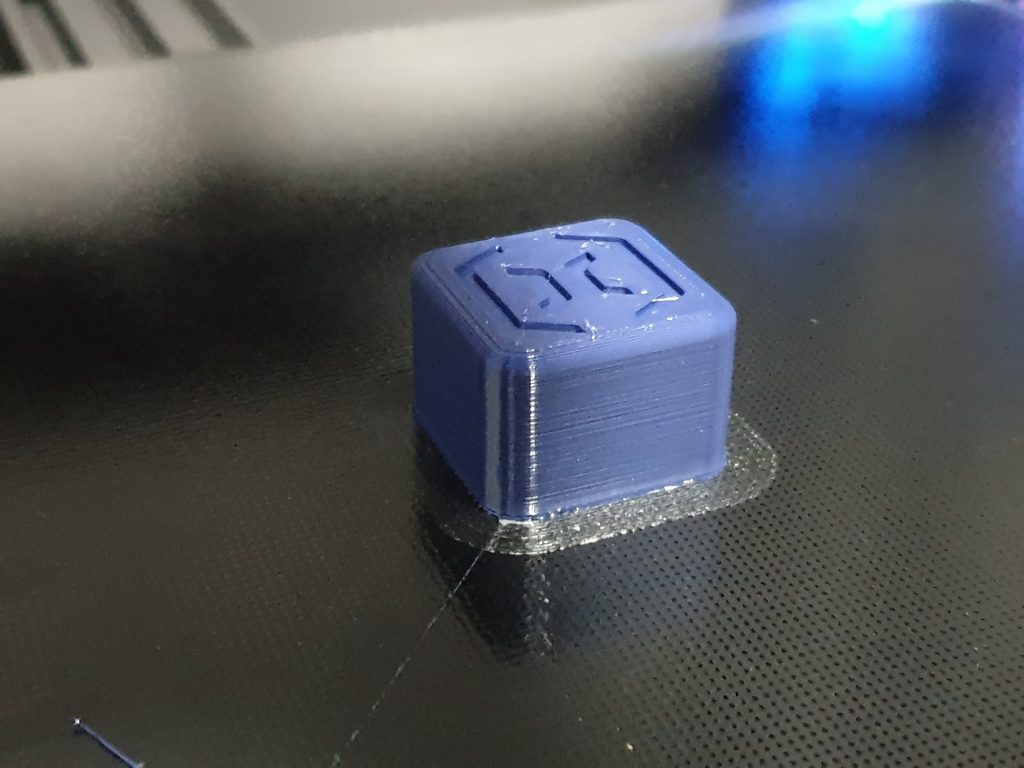
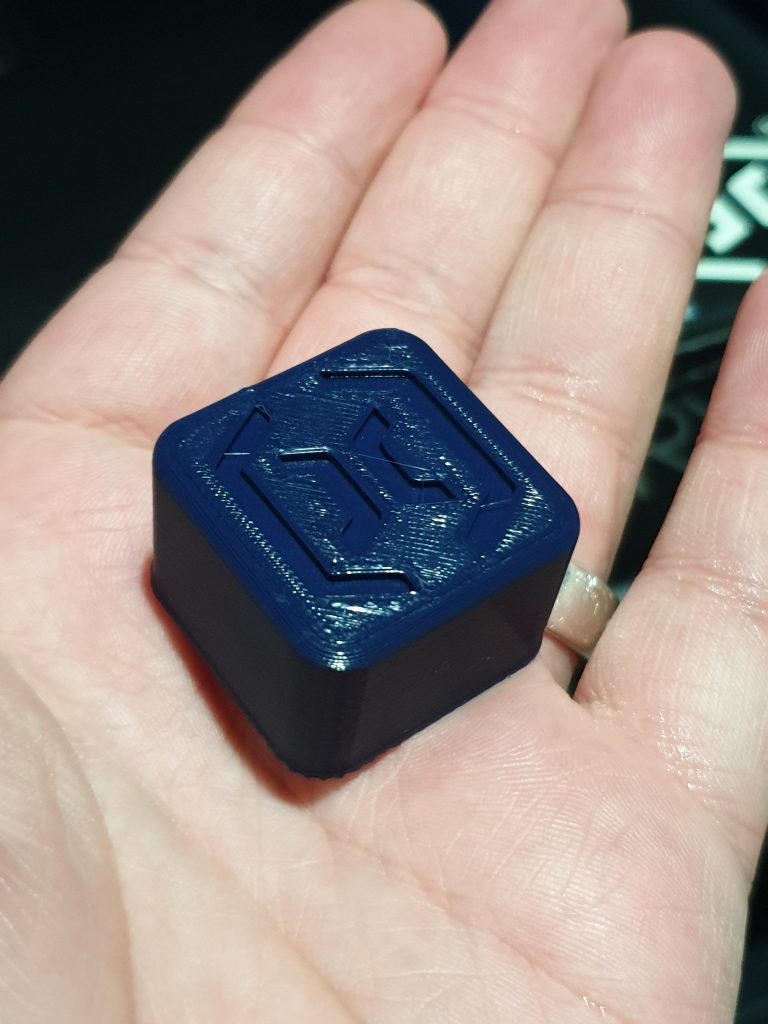
FInal Thoughts
This printer held up Artillerys reputation of making a refined printer, and it’s good to see they are still working on new designs and making improvements here and there. Their previous generation of printers work completely fine and they could have just kept selling them, so it’s good to see them wanting to innovate and improve things.
Should you buy this printer? If you are looking for a premium printer with all the bells and whistles, and in a 300×300 format then I’d definitely have this printer at the top of my list! In the past I have recommended the Artillery Genius and Sidewinder X1 to many, and I think the sidewinder X2 and the also newly our Genius V2 will replace this recommendation.
Now that I am back in the review game (I have another printer at home to build and review) hopefully I can get my hands on a Genius V2!
Let me know what you think of this printer.
Dave
Leave a Comment